Unlocking Excellence in Injection Mold Manufacturing with Leading Metal Fabricators
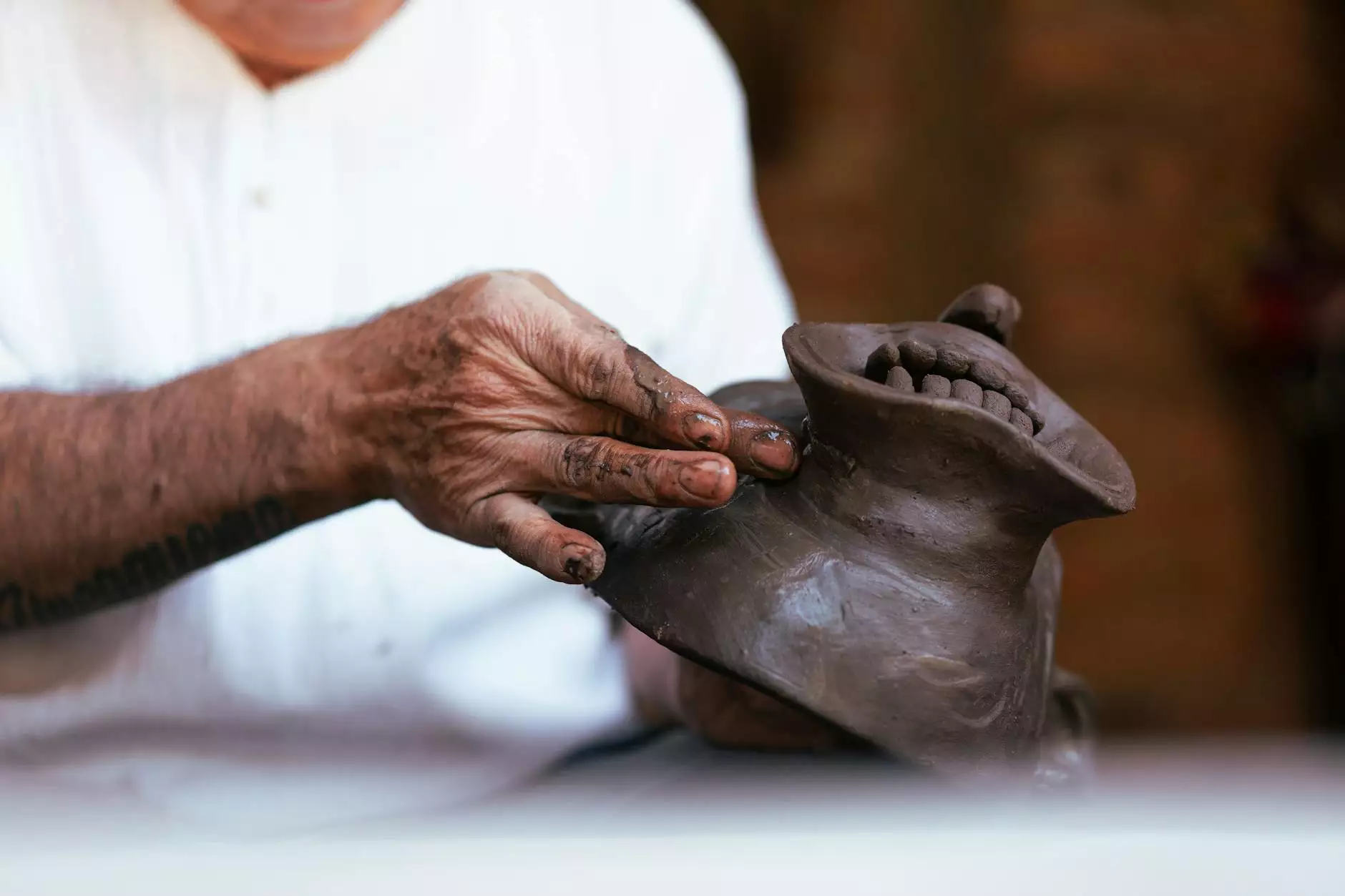
In today's highly competitive manufacturing landscape, the ability to produce high-quality, precise, and durable molds is paramount. Injection mold manufacturing stands at the core of producing complex plastic components for various industries including automotive, consumer electronics, healthcare, and home appliances. Companies like Deep Mould exemplify innovation and expertise in metal fabricators dedicated to delivering top-tier mold solutions that meet and exceed client expectations.
Understanding the Significance of Injection Mold Manufacturing
Injection mold manufacturing is a specialized subset of metal fabrication focused on creating precision molds that facilitate efficient and high-volume plastic injection molding processes. These molds are intricate, requiring meticulous design and manufacturing techniques to ensure they produce parts with impeccable accuracy, consistency, and surface finishes.
High-quality molds translate directly into product excellence, cost efficiency, and shorter time-to-market. The process involves collaboration between designers, materials engineers, and manufacturing experts who meticulously plan and execute every phase of mold creation, from conceptual design to final testing.
Core Components of Injection Molds Crafted by Metal Fabricators
- Core and Cavity: The fundamental parts that shape the interior and exterior of the finished product. Their precision directly impacts the dimensional accuracy and surface quality.
- Runner System: Channels that guide the molten material into the mold cavities. Proper design ensures uniform filling and minimizes defects.
- Temperature Control System: Integrated channels for cooling that ensure consistent mold temperature, reducing cycle times and defect rates.
- Locking Mechanisms: Components that keep the mold closed under high pressure during injection, maintaining the integrity of the part shape.
- Ejection System: Elements designed to safely and efficiently eject finished parts without damage or deformation.
The Role of Metal Fabricators in Injection Mold Manufacturing
Leading metal fabricators like Deep Mould leverage advanced manufacturing technologies and materials to produce molds that meet stringent industry standards. Their expertise encompasses:
Precise Material Selection
Choosing the right metals—such as high-grade tool steels, aluminum alloys, or beryllium copper—is critical for mold durability, thermal conductivity, and ease of machining. Top fabricators understand the nuances of material properties to optimize mold performance.
Advanced Manufacturing Techniques
- CNC Machining: Computer-controlled cutting tools create intricate mold components with micron-level precision.
- Electrical Discharge Machining (EDM): Used for complex, hard-to-machine features, EDM ensures detailed craftsmanship and fine surface finishes.
- Surface Treatment: Coatings like PVD or nitriding enhance mold lifespan and release properties.
- 3D Printing: Rapid prototyping and complex cavity creation are made possible with additive manufacturing technologies.
Quality Control and Testing in Injection Mold Manufacturing
High standards in injection mold manufacturing are maintained through rigorous quality control processes, including:
- Dimensional inspections using coordinate measuring machines (CMMs)
- Visual and surface finish assessments
- Prototype testing to verify functionality and ease of injection
- Cycle testing to evaluate durability and thermal performance
These steps ensure each mold adheres to strict specifications, facilitating flawless production runs and minimizing costly rework or downtime.
Innovations Driving the Future of Injection Molding
The realm of injection mold manufacturing is continually advancing, propelled by technological innovations such as:
- Smart Molds: Integration of sensors for real-time monitoring of temperature, pressure, and wear, enabling predictive maintenance and enhanced process control.
- Modular Mold Designs: Allowing quick modifications to accommodate different product variants, reducing lead times and tooling costs.
- Surface Finishing Technologies: Improved techniques like laser texturing and nanocoatings provide better aesthetic and functional surface properties.
- Eco-Friendly Materials and Processes: Emphasis on sustainability through recyclable mold materials and energy-efficient manufacturing methods.
Why Partnering With a Trusted Metal Fabricator Like Deep Mould Matters
When it comes to injection mold manufacturing, the difference lies in the expertise, reputation, and technological capabilities of your manufacturing partner. Choosing a reliable metal fabricator ensures:
- Superior Quality: Consistently producing highly precise and durable molds.
- Customization: Tailored solutions that align exactly with your product specifications and production needs.
- Cost-Efficiency: Optimized processes that reduce waste, cycle times, and overall costs.
- Fast Turnaround: Expertise in managing complex projects under tight schedules.
- Continuous Innovation: Leveraging the latest technology to improve mold performance and lifespan.
Deep Mould exemplifies these qualities by offering comprehensive metal fabrication services that cater specifically to injection mold manufacturing. Their dedicated team of engineers design, produce, and test molds that enable clients to stay ahead in competitive markets.
Ensuring Sustainability and Longevity in Injection Mold Production
Sustainable manufacturing practices are increasingly vital in the modern industrial environment. Leading metal fabricators incorporate eco-friendly materials, waste reduction strategies, and energy-efficient machinery to minimize environmental impact while maintaining high standards of quality. Additionally, durable mold designs extend service life, reducing the need for frequent replacements and further supporting sustainability goals.
The Complete Lifecycle of Injection Molds
An efficient injection mold manufacturing process considers the entire lifecycle, including:
- Design and Development: Precise CAD modeling and simulation to optimize performance.
- Material Selection and Machining: Using the best materials and advanced techniques to produce complex mold components.
- Assembly and Testing: Assembling all parts with exacting standards and conducting rigorous testing.
- Production and Maintenance: Ensuring continuous operation through preventive maintenance and timely repairs.
- Recycling and Reconditioning: Reusing or reconditioning molds at end-of-life to maximize value and sustainability.
Conclusion: The Path to Manufacturing Success with Expert Metal Fabricators
By prioritizing injection mold manufacturing that combines cutting-edge technology, high-quality materials, and rigorous quality control, businesses can achieve unparalleled production efficiency and product quality. Partnering with experienced metal fabricators like Deep Mould ensures your projects are handled with precision, innovation, and reliability.
In an era where manufacturing excellence defines market leadership, investing in superior mold production is not just beneficial—it is essential. Embrace the future of metal fabrication and injection mold manufacturing with confidence, and set your business apart through unmatched quality and technological prowess.
Contact Deep Mould for Your Injection Mold Manufacturing Needs
If you seek a trusted partner to deliver industry-leading injection mold manufacturing services, reach out to Deep Mould. Our commitment to precision and innovation makes us your ideal choice for all your mold fabrication requirements.