The Importance and Innovation of Oil Cooler Factories
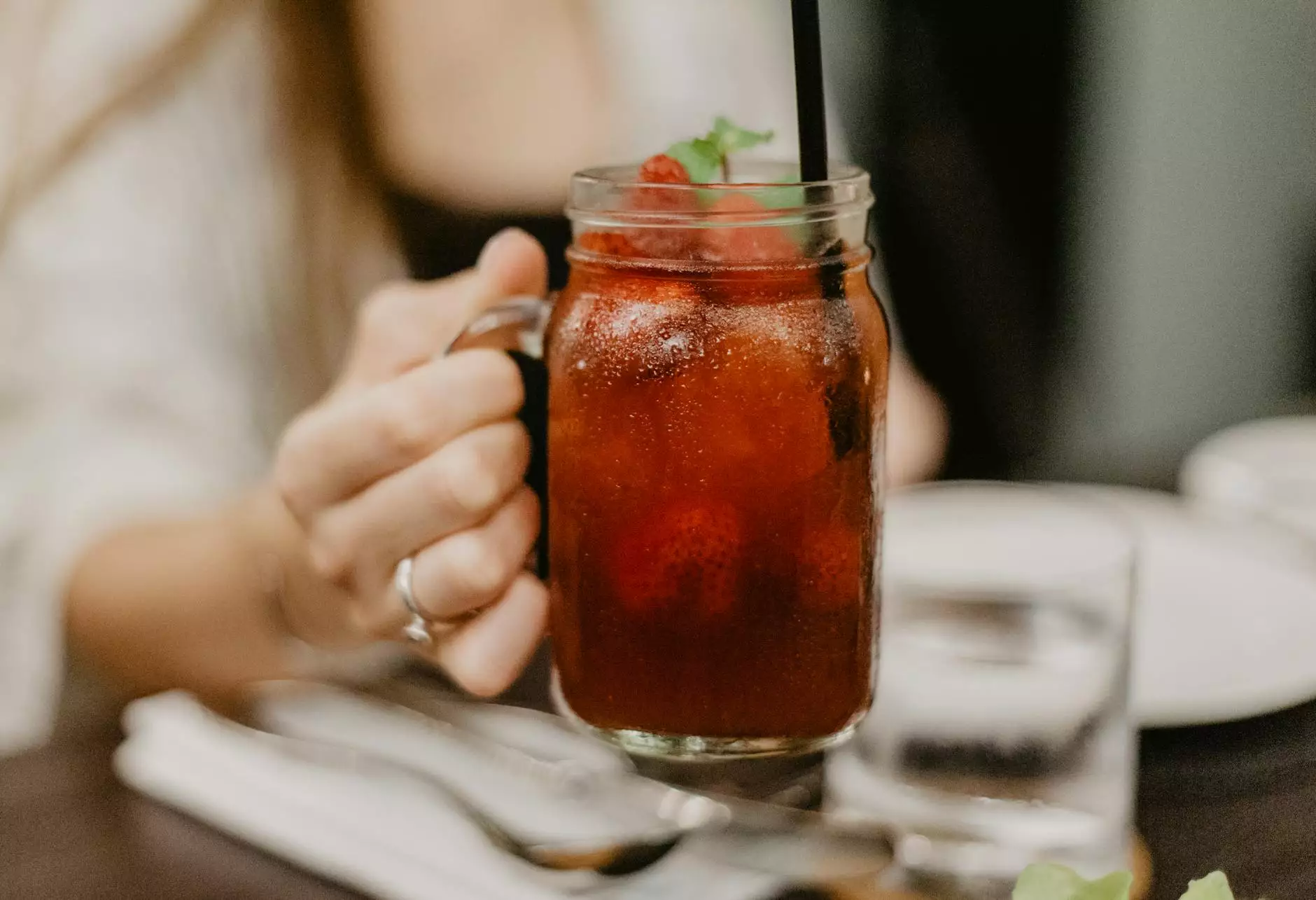
In the ever-evolving world of diesel engine parts, the role of an oil cooler factory cannot be understated. These facilities are not just manufacturers but also critical contributors to the longevity and efficiency of diesel engines. In this article, we will explore the significance of oil coolers, the manufacturing process, technology, and their impacts on diesel engines, particularly in relation to client-diesel.com.
Understanding Oil Coolers
Oil coolers are essential components designed to regulate the temperature of engine oil, ensuring optimal performance. By maintaining the right temperature, oil coolers protect the engine from excessive heat, which can lead to failures. Here's why oil coolers are vital:
- Heat Management: They help in dissipating heat generated from the engine, maintaining an optimal operating temperature.
- Engine Efficiency: By keeping oil at an ideal temperature, coolers enhance the overall efficiency of the engine.
- Longevity: They prevent wear and tear on engine components, prolonging the life of diesel engines.
- Environmental Impact: Efficient engines burn fuel more completely, reducing emissions.
The Manufacturing Process of Oil Coolers
The journey of an oil cooler starts at the oil cooler factory. Here’s a detailed look at the manufacturing process:
1. Material Selection
Oil coolers are typically made from materials that offer excellent thermal conductivity and corrosion resistance. Common materials include:
- Aluminum: Lightweight and excellent for heat dissipation.
- Brass: Offers durability and corrosion resistance.
- Copper: Provides exceptional thermal conductivity.
2. Design and Engineering
Advanced design software is utilized to create oil cooler models that efficiently manage heat transfer. Engineers focus on:
- Flow Dynamics: How oil flows through the cooler impacts efficiency.
- Surface Area: Greater surface area improves heat transfer.
- Compactness: Ensuring the cooler fits into designated engine spaces without compromising performance.
3. Production Techniques
Once designed, the oil coolers are produced using several manufacturing techniques:
- Extrusion: Used to shape aluminum into the required profiles.
- Welding: Components are welded together to form a robust and durable product.
- Testing: Each unit undergoes rigorous testing for pressure, leakage, and performance.
4. Quality Control
Before reaching the market, oil coolers are subject to a series of quality assurance checks to ensure they meet industry standards. This includes:
- Pressure Testing: Ensures that the cooler can withstand operational pressures.
- Visual Inspections: Identifies any physical defects.
- Performance Benchmarking: Assesses how well the cooler performs under simulated conditions.
Innovation in Oil Cooler Manufacturing
The world of manufacturing is continuously evolving, and oil cooler factories are at the forefront of innovation. Current trends include:
1. Use of Advanced Materials
New composites and enhanced aluminum alloys are being utilized to create even more efficient oil coolers that offer greater durability while reducing weight.
2. Integration of Technology
Modern factories are incorporating automation and AI to improve manufacturing processes:
- Robotic Assembly: Increases precision and reduces human error.
- IoT Integration: Enables real-time tracking of production efficiency and quality control.
3. Environmental Considerations
Sustainability is becoming a priority. Factories are implementing techniques that reduce waste and lower carbon emissions during manufacturing.
The Impact of Oil Coolers on Diesel Engines
The efficiency of diesel engines is significantly influenced by the quality of oil coolers produced in an oil cooler factory. Here’s how:
1. Performance Enhancement
By maintaining optimal oil temperature, engines can perform better and maintain power output, allowing for:
- Improved Towing Capacity: Essential for heavy-duty diesel engines.
- Better Fuel Efficiency: Cooler oil leads to less energy wastage.
2. Reduced Maintenance Costs
Engines equipped with high-quality oil coolers often experience:
- Fewer Breakdowns: Reduced wear and tear translates to lower failure rates.
- Longer Service Intervals: Less frequent oil changes and overall engine maintenance.
3. Compliance with Environmental Standards
With stricter environmental regulations, efficient oil coolers help manufacturers comply with emissions standards, contributing to a greener footprint.
The Future of Oil Cooler Factories
The future looks promising for oil cooler factories as the demand for diesel engine parts continues to evolve. With advancements in technology, a strong focus on sustainability, and increasing customer expectations, these factories must innovate continuously. Here are some potential developments:
- Smart Oil Coolers: Integration of sensors that monitor oil temperature and pressure in real time.
- Customization: Offering tailored solutions based on specific engine requirements.
- Global Expansion: Expanding operations to meet the growing demand in emerging markets.
Conclusion
In the dynamic industry of diesel engine parts, oil cooler factories play a vital role in manufacturing essential components that ensure the longevity, efficiency, and environmental compliance of diesel engines. With the ongoing innovations in production techniques and materials, these factories are set to meet the future demands of a rapidly changing market. As businesses like client-diesel.com continue to push the boundaries, the significance of high-quality oil coolers will only become more pronounced, driving the industry forward.