Transforming Construction with Prefab Building
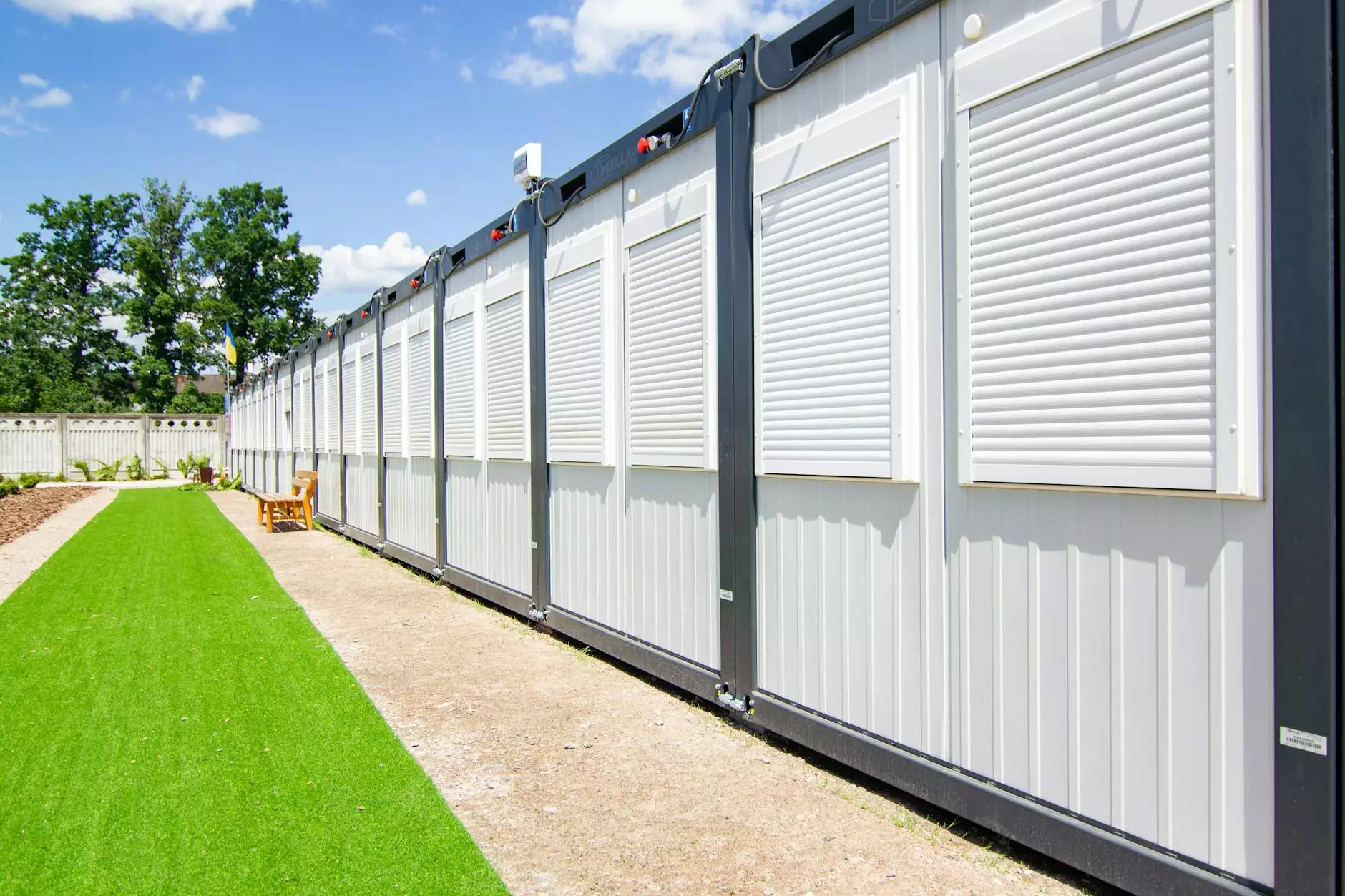
In today’s fast-paced world, businesses are always on the lookout for ways to enhance efficiency and reduce costs. One innovative approach gaining traction in the construction industry is prefab building. This method not only streamlines the construction process but also ensures high-quality results, making it a favorite among contractors and developers alike. In this comprehensive article, we will dive deep into the world of prefab building, examining its benefits, applications, and why it has become an essential choice for modern-day construction projects.
What is Prefab Building?
Prefab building, short for prefabricated building, refers to structures that are manufactured off-site in advance, usually in standard sections that can be easily transported and assembled on location. This technique has been around for several decades but has recently seen a revival due to advances in technology and growing demand for efficient construction solutions.
Key Benefits of Prefab Building
Prefab building offers numerous advantages that can significantly contribute to the success of construction projects. Here are some of the standout benefits:
- Time Efficiency: One of the primary advantages of prefab building is the reduced construction time. Components are built in a controlled environment simultaneously as site preparation happens, ensuring that the project is completed quicker than traditional methods.
- Cost-Effectiveness: By reducing the time and labor required for construction, prefab buildings can significantly lower overall costs. Additionally, bulk purchasing of materials leads to savings that can be passed on to clients.
- Quality Control: Since prefab components are manufactured in a factory setting, they are subject to stringent quality control processes. This results in higher quality structures with fewer defects, minimizing the need for repairs and maintenance.
- Flexibility and Customization: Prefab building allows for a high degree of customization, enabling contractors to meet specific client needs while still adhering to timelines and budgets.
- Environmental Benefits: With a more efficient construction process, prefab buildings generate less waste and use fewer resources compared to traditional building methods, making them a more sustainable option.
Applications of Prefab Building
The versatility of prefab building means it can be utilized in a wide variety of applications. Below are some common uses:
Residential Construction
Prefab homes are increasingly popular due to their affordability and the speed at which they can be constructed. These homes can be fully customized to meet the homeowner's specifications, from layout and design to materials and finishes.
Commercial Spaces
Many businesses are turning to prefab construction for offices, retail spaces, and even restaurants. The rapid setup allows businesses to start operations sooner, while standardization can help keep costs down.
Industrial Facilities
Warehouses and manufacturing plants can benefit from prefab building's durability and customizable layouts. Prefabricated structures can be designed to meet specific industry needs while reducing construction time significantly.
Why Choose Module-T for Your Prefab Building Needs?
If you're considering a prefab building solution, choosing the right contractor is essential. Module-T stands out in the industry for several reasons:
- Expertise: With years of experience in the industry, Module-T has a proven track record of successful projects and satisfied clients.
- Quality Materials: We source materials from trusted suppliers, ensuring that all components meet high standards of quality and durability.
- Customer-Centric Approach: Our team works closely with clients to customize solutions that exactly match their vision and requirements.
- Innovative Technology: By utilizing the latest technology in prefab construction, we enhance efficiency, accuracy, and overall project delivery.
The Process of Prefab Building
1. Design Phase
Every successful project begins with a thoughtful initial design. The module design process allows for flexibility and adaptability, accommodating a client’s needs while adhering to architectural guidelines.
2. Manufacturing
Once the design is finalized, components are fabricated in a controlled environment. This phase includes precision cutting and assembly of the pieces that will form the building structure. Quality assurance ensures that everything meets the necessary standards before shipping.
3. Site Preparation
While the prefab components are being manufactured, site preparation occurs simultaneously. This includes clearing the land, laying foundations, and ensuring utilities are in place.
4. Transportation and Assembly
After the components are manufactured, they are transported to the construction site. Our team assembles the pieces on location, with careful attention to detail to ensure that everything fits perfectly and is structurally sound.
5. Finishing Touches
The final phase involves completing the interior and exterior finishes, which can be as customizable as the design allows.
Cost Considerations
The cost of prefab building can vary widely based on a variety of factors. Understanding these elements can help you budget effectively:
- Size of the Project: Larger projects tend to benefit more from the economies of scale available with prefab building.
- Location: Costs can increase if the construction site is in a remote location due to transportation of materials and components.
- Custom Features: While many prefab structures come with standard configurations, adding custom elements will impact your budget.
- Foundation Requirements: The type of foundation needed can also affect the overall cost, depending on soil conditions and local regulations.
Overcoming Common Misconceptions about Prefab Buildings
Despite the growing acceptance of prefab construction, there are still some misconceptions that need to be addressed:
Misconception #1: Inferior Quality
Many believe that prefab buildings lack the quality of traditional construction. However, the reality is that modern prefab processes use high-quality materials and strict manufacturing standards that often exceed traditional building quality.
Misconception #2: Limited Design Options
Contrary to popular belief, prefab buildings offer a wide range of design options. Clients can choose layouts, materials, and finishes that best suit their aesthetic preferences and functional needs.
Misconception #3: Poor Resale Value
Some potential buyers mistakenly believe that prefab homes won’t appreciate as much in value as traditionally built homes. However, a well-constructed prefab home can hold its value and even appreciate in a healthy real estate market.
Final Thoughts on Prefab Building
The shift towards prefab building marks a significant evolution within the construction industry. Its combination of efficiency, affordability, quality, and sustainability makes it a compelling choice for contractors and developers. As the market continues to embrace innovative construction techniques, prefab buildings will undoubtedly play a crucial role in shaping the landscape of modern architecture.
If you are considering a construction project and want to explore the advantages of prefab building, reach out to Module-T today. Our team of experts is ready to help you navigate your options, ensuring that your dream project becomes a reality.
Contact Us
For more information about how we can assist you with prefab building solutions, please visit our website at module-t.com or contact us directly. Let’s build something great together!